The Inspection Company Ltd. works according to the international quality standards (AQL), norms, and regulations. This allows customers to understand each report quickly and easily.
AQL - Acceptable Quality Level
The AQL-Standard provides a basis for the clients to decide on how they will proceed. Our inspectors work with the ISO 2859 tables and evaluate the AQL of the inspected product. The ISO 2859 refers to a U.S. standard with equivalents in the national and international standard-setting body (ANSI /ASQC Z 1.4, ISO 2859, NF06 -022, BS 6001, DIN 40080). We use the proven method of Acceptable Quality Level (AQL) to conduct product inspection ANSI/ASQ Z1.4-2008 and MIL-STD 105E Standard for sampling.
The acceptance quality level (AQL) is internationally defined as the maximum defective percentage (or the maximum number of defects per hundred units) that, for the purpose of sampling inspection, can be considered satisfactorily as a process average.
We will select a sampling size quantity (according to the AQL tables), and give you a recommendation according to the number of defects found (critical, major, minor defects). The result will show if you would rather accept or reject the shipment.
Example :
For a lot of 5000 units, with a General Inspection Level II (this is the most commonly used Level ) you will find the sample size code letter "L"? see Table I.
In Table B we find the sample size ("L") will be 200 units. TIC will now inspect 200 units of this production lot. When applying an AQL level of 2.5 (Table II) you’ll find that the corresponding acceptance number is 10. If TIC finds 11 defects the shipment should be rejected by the customer.
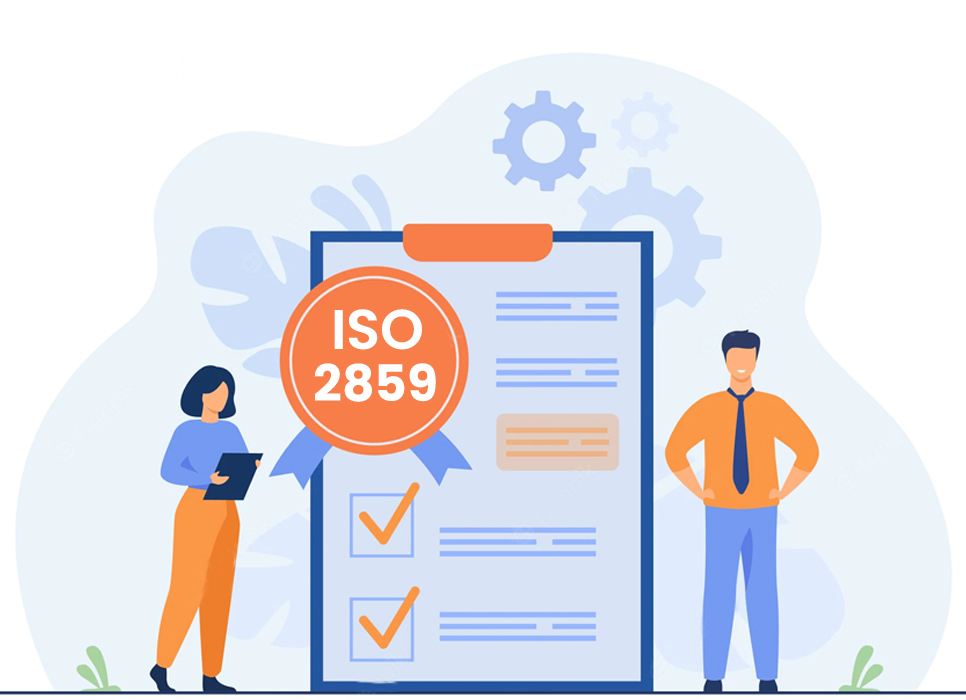
Table I - Sample size code letters
Lot or Batch Size | Normal Inspection Levels | Special Inspection Levels | |||||
---|---|---|---|---|---|---|---|
I | II | III | S1 | S2 | S3 | S4 | |
2 to 8 | A | A | B | A | A | A | A |
9 to 15 | A | B | C | A | A | A | A |
16 to 25 | B | C | D | A | A | D | D |
26 to 50 | C | D | E | A | B | B | C |
51 to 90 | C | E | F | B | B | C | C |
91 to 150 | D | F | G | B | B | C | D |
151 to 280 | E | G | H | B | C | D | E |
281 to 500 | F | H | J | B | C | D | E |
501 to 1,200 | G | J | K | C | C | E | F |
1,201 to 3200 | H | K | L | C | D | E | G |
3,201 to 10,000 | J | L | M | C | D | F | G |
10,001 to 35,000 | K | M | N | C | D | F | H |
35,001 to 150,000 | L | N | P | D | E | G | J |
150,001 to 500,000 | M | P | Q | D | E | G | J |
500,001 and over | N | Q | R | D | E | H | K |
How to Read the AQL Table?
Reading the AQL table involves two primary tables. The first table helps determine the "code letter" based on the lot size and inspection level. This code letter then indicates the sample size and the maximum number of acceptable defects.
Table II - Single sample plans for normal inspection (Master Table)
Sample Size Code Letter | Sample Size | Acceptable Quality Levels (Normal Inspection) | |||||||||||||||||||||||
---|---|---|---|---|---|---|---|---|---|---|---|---|---|---|---|---|---|---|---|---|---|---|---|---|---|
0.065 | 0.10 | 0.15 | 0.25 | 0.4 | 0.65 | 1.0 | 1.5 | 2.5 | 4.0 | 6.5 | 10 | ||||||||||||||
Ac | Re | Ac | Re | Ac | Re | Ac | Re | Ac | Re | Ac | Re | Ac | Re | Ac | Re | Ac | Re | Ac | Re | Ac | Re | Ac | Re | ||
A | 2 | 0 | 1 | ||||||||||||||||||||||
B | 3 | 0 | 1 | ||||||||||||||||||||||
C | 5 | 0 | 1 | 1 | 2 | ||||||||||||||||||||
D | 8 | 0 | 1 | 1 | 2 | 2 | 3 | ||||||||||||||||||
E | 13 | 0 | 1 | 1 | 2 | 2 | 3 | 3 | 4 | ||||||||||||||||
F | 20 | 0 | 1 | 1 | 2 | 2 | 3 | 3 | 4 | 5 | 6 | ||||||||||||||
G | 32 | 0 | 1 | 1 | 2 | 2 | 3 | 3 | 4 | 5 | 6 | 7 | 8 | ||||||||||||
H | 50 | 0 | 1 | 1 | 2 | 2 | 3 | 3 | 4 | 5 | 6 | 7 | 8 | 10 | 11 | ||||||||||
J | 80 | 0 | 1 | 1 | 2 | 2 | 3 | 3 | 4 | 5 | 6 | 7 | 8 | 10 | 11 | 14 | 15 | ||||||||
K | 125 | 0 | 1 | 1 | 2 | 2 | 3 | 3 | 4 | 5 | 6 | 7 | 8 | 10 | 11 | 14 | 15 | 21 | 22 | ||||||
L | 200 | 0 | 1 | 1 | 2 | 2 | 3 | 3 | 4 | 5 | 6 | 7 | 8 | 10 | 11 | 14 | 15 | 21 | 22 | ||||||
M | 315 | 1 | 2 | 2 | 3 | 3 | 4 | 5 | 6 | 7 | 8 | 10 | 11 | 14 | 15 | 21 | 22 | ||||||||
N | 500 | 1 | 2 | 2 | 3 | 3 | 4 | 5 | 6 | 7 | 8 | 10 | 11 | 14 | 15 | 21 | 22 | ||||||||
P | 800 | 1 | 2 | 2 | 3 | 3 | 4 | 5 | 6 | 7 | 8 | 10 | 11 | 14 | 15 | 21 | 22 | ||||||||
Q | 1250 | 2 | 3 | 3 | 4 | 5 | 6 | 7 | 8 | 10 | 11 | 14 | 15 | 21 | 22 | ||||||||||
R | 2000 | 3 | 4 | 5 | 6 | 7 | 8 | 10 | 11 | 14 | 15 | 21 | 22 | ||||||||||||
: Use the first sampling plan below the arrow. if sample size equals or exceeds lot size, carry out 100% inspection | |||||||||||||||||||||||||
: Use the first sampling plan above the arrow | |||||||||||||||||||||||||
Ac: Acceptance number | |||||||||||||||||||||||||
Re: Rejection number |
How to Read This Table?
For example, if your lot size is between 3,201 and 10,000 pieces and your inspection level is "II", the code letter would be "L". This means you need to randomly select 200 pieces from the lot size. If your AQL is set at 2.5% for major defects and 4.0% for minor defects, the products are acceptable if no more than 10 major defects and no more than 14 minor defects are found. For instance, finding 15 major defects and 12 minor defects would result in rejection, while finding 3 major defects and 7 minor defects would be acceptable.
Frequently Asked Questions (FAQ)
- Critical defects: These defects can cause safety hazards or make the product unsafe to use.
- Major defects: These defects significantly affect the product’s appearance or functionality but do not pose a safety hazard.
- Minor defects: These are small defects that do not affect the product’s overall usability or safety.